Open Communication is the Key to Successful Business Lending
Gordie Howe International Bridge
Progress remains steady on this impressive project that will be among the longest cable-stayed bridges in North America.
By Lisa Kopochinski
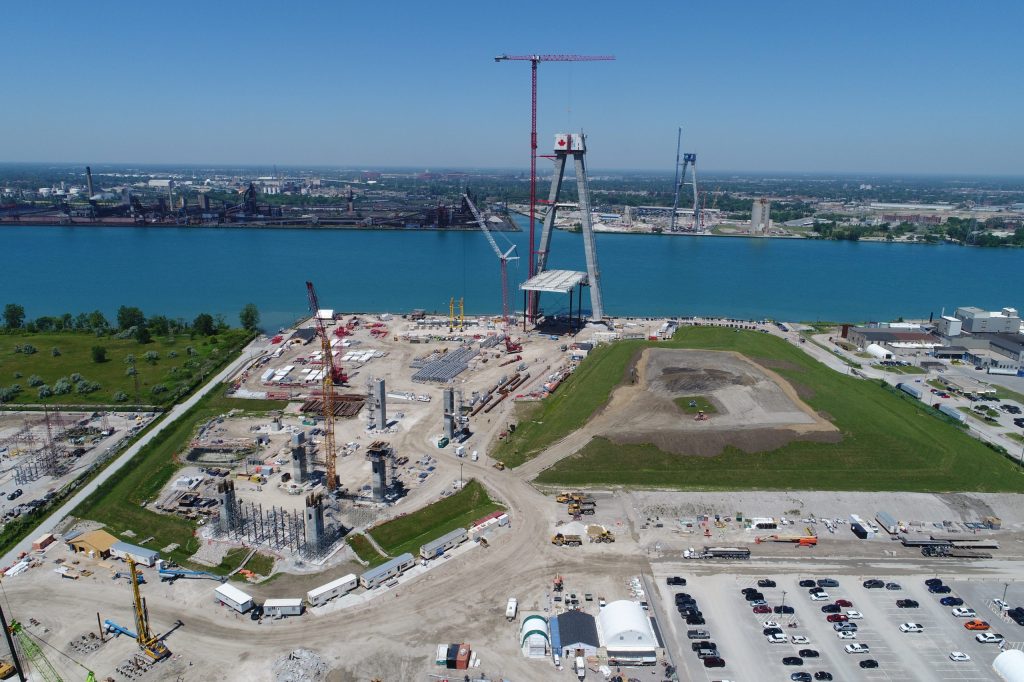
Canada bridge tower legs and back span piers in July 2022
Photos courtesy of WDBA
What do you get when you combine one of the world’s greatest hockey players of all time and an impressive structure? The Gordie Howe International Bridge project, of course.
With a completion date slated for 2024, the Gordie Howe International Bridge will connect Windsor, Ont., to Detroit, Mich., and be among the longest cable-stayed bridge in North America – spanning 2.5 kilometres. It will also be the fifth longest cable-stayed bridge in the world.
The Windsor-Detroit Bridge Authority (WDBA) is delivering this $5.7-billion project, which began in October 2018. The project is being carried out through a public-private partnership. The Canadian Government (through its Crown corporation), WDBA and Bridging North America (BNA), WDBA’s private partner responsible for designing, building, financing, operating and maintaining the Canadian and U.S. Ports of Entry and bridge.
The project has four components:
- The bridge
- The Canadian entry point and customs plaza
- The U.S. entry point
- Linking Highway 401 in Ontario to Interstate
- 75 in Michigan
The bridge will accommodate three Canadian-bound lanes and three U.S.-bound lanes for cars and commercial traffic.
There are several unique features of the Gordie Howe International Bridge project. For instance, having the bridge piers located on land, the bridge’s main section will extend over the Detroit River and be constructed using a technique called the unbalanced cantilever system or stick build.
“In response to public consultation and feedback, the project will also include a dedicated multi-use path that will accommodate pedestrians and cyclists. The integration of the multi-use path will benefit the communities, as it will support active transportation and a healthy lifestyle, as well as enhance cycle tourism across the border,” said WDBA director of communications Tara Carson.

Project Challenges
All projects have their share of technical and logistical challenges and one of this magnitude is no exception.
Carson says one of the bridge team’s challenges was the approach to the bridge’s construction.
“Original methods followed the traditional balanced cantilever construction. However, obstructions in early days, including limited water access, deep soft clay and winter weather caused BNA to revisit this erection method to mitigate potential delays,” said Carson.
Additional project challenges included:
- Execution of deep foundation works within the immediate vicinity of the Detroit River requiring the implementation of temporary seawall protection (scour protection).
- Artesian groundwater conditions requiring the implementation of groundwater control plans, as well as the implementation of a special underwater concrete mix design for drilled shaft construction.
- Environmental challenges requiring fisheries management and specific management of waste, spoils and concrete washout, hydrogen sulphide gas procedure, and specific erosion and sediment plans.
- Adverse soil conditions requiring the implementation of a group of three-metre diameter drilled shafts with permanent steel underground water.
Deep Foundation Aspect
Regarding the deep foundation aspect within the scope of the entire construction project, BNA uses some of the following materials: three-metre diameter drill shafts, steel casing 19-millimetre wall thickness, reinforcing steel grade 400W and 41.4 MPa concrete.
“Each of the tower legs’ foundations are built onto six drilled shafts with a diameter of three metres and a depth of approximately 36 metres down to the bedrock,” said Carson.
“All of the six back span piers are built onto one drilled shaft with a three-metre depth approximately 36 metres down to the bedrock. GFL was the main subcontractor for drilled shaft construction.”
The BNA completed a bi-directional compressive load test (using O-Cell) on a nonproduction shaft built with the same means and methods as the production shafts to assess the challenges brought on by the design environment, and geology/soil, noise and vibration reduction. In addition, load test results were used to determine rock-socket lengths for the production shafts.
Equipment Used
Building North America and its subcontractors are using a wide variety of equipment on the impressive $5.7-billion Gordie Howe International Bridge project, which began in 2018 and is scheduled for completion in 2024. The team used steel piles to support the ramps connecting the U.S. Port of Entry to I-75 and the road and pedestrian bridges over I-75 being constructed as part of the Michigan Interchange work for the project. Some of the equipment used includes:
- Drilling and pressure grouting equipment
- Bauer BG40 drilling rig
- Manitowoc 1600 crawler crane (main crane)
- Manitowoc 2250 service crane
- ICE 44-50 vibratory hammer
- CAT IT14G loader
- Multiple diameter rock augers
- Soil auger
- Multiple diameter core barrels for rock-socket drilling
- Airlifting equipment
- Elevating working platforms (Genie)
- 36-metre mobile concrete pumps with tremie lines for concrete placement
- Concrete mixer trucks
Environment and Sustainability
Environmental sustainability measures have also remained at the forefront. For example, the Gordie Howe International Bridge project is an example of sustainable infrastructure that is socially, environmentally and economically responsible. Moreover, it protects communities on both sides of the border from the effects of climate change.
“The project will be a high-performance, sustainable building and infrastructure project, designed for resource efficiency and cost-effectiveness (both in construction and operation) with healthy and productive environments,” said Carson.
“Emphasis is being placed on measurable high-performance green building and infrastructure strategies and processes, integrating products, components and systems, improving building performance by significantly reducing energy consumption, increasing facility flexibility, and improving user comfort and satisfaction.”
WDBA and BNA have earned a prestigious Envision Platinum Award for this once-in-a-generation project. This certification is the highest possible distinction from the Institute for Sustainable Infrastructure, which recognizes efforts to achieve sustainable development and environmental performance standards at every stage of an infrastructure project, from design to construction and implementation.
The Gordie Howe International Bridge project includes a comprehensive environmental program that addresses over 450 conditions identified in the bi-national environmental assessment process.
The Gordie Howe International Bridge project includes a comprehensive environmental program that addresses over 450 conditions identified in the bi-national environmental assessment process. It also consists of a community benefits plan with $20 million in direct community investments that create opportunities to enhance economic, social and environmental conditions – from trail connections to road and park improvements, home repairs and arts and culture initiatives. Both plans were developed because of hundreds of consultation meetings with Michigan and Ontario residents, Indigenous Peoples, business owners, and community and municipal leaders.
BNA was required to create and implement a sustainable management policy as part of the project agreement. The policy used a roadmap to help achieve performance targets for LEED and Envision certifications.
Safety First

Carson says safety has been at the forefront of this project and will remain until completion.
“Safety is a core value at BNA, and their success stems from the commitment of our joint BNA/WDBA health and safety teams and all staff. We have a great video called ‘Nine Questions with Health and Safety Managers’ that highlights the approach to safety that is being undertaken.”
Carson says safety has been at the forefront of this project and will remain until completion.
The team is also proud to have received the Infrastructure Health and Safety Association John M. Beck Award in 2021. This award recognizes the contributions a project-based Joint Health and Safety Committee in the Ontario construction industry has made to health and safety in the previous year.
“To date, this project has completed over three million hours without a lost time injury,” Carson said.
Calgary’s Thriving Tech Scene
In spite of the pandemic – or because of it – the city’s technology sector continues its impressive growth.
By Lisa Kopochinski
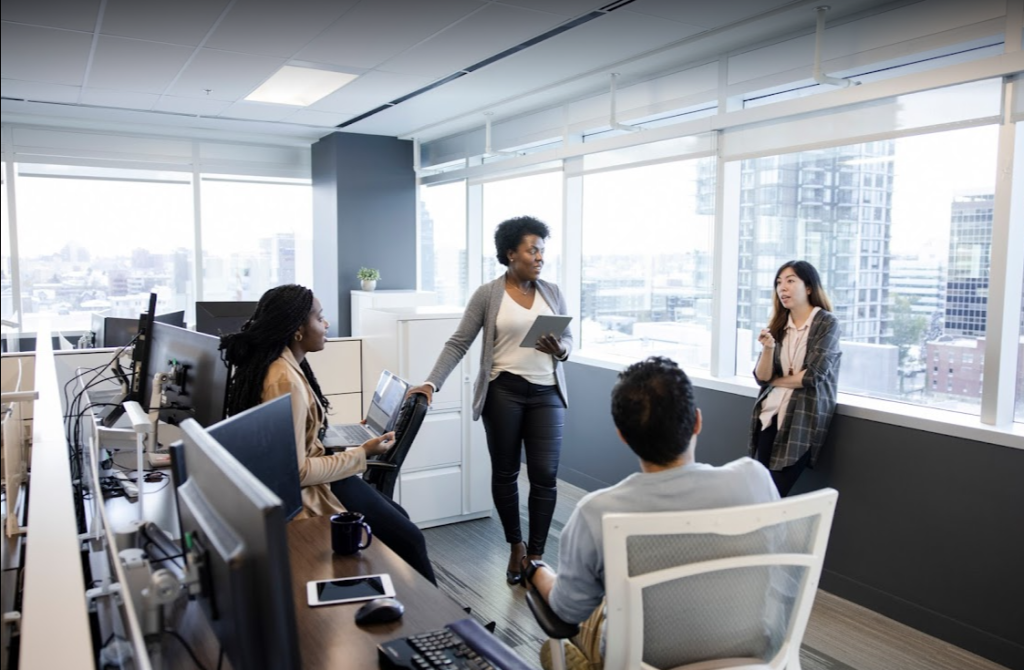
Calgary’s booming technology scene is exactly that – booming. Even with the pandemic nearly behind us, the market has remained strong.
For example, as part of its $17 billion investment in operations, infrastructure and spectrum across Alberta through 2026, TELUS recently opened TELUS Sky, a new state-of-the art headquarters in downtown Calgary. Standing 60 stories high and spanning 750,000 square feet of office and retail space, this project achieved LEED platinum certification.
“Our $400 million development continues our legacy of making powerful contributions to advance the economic strength and social vitality of both the city of Calgary and the province of Alberta,” says TELUS president and CEO Darren Entwistle in a GlobeNewswire press release.
“Over the past century, TELUS has invested $60 billion in network infrastructure, operations and technology across the province, and will create a further 8,500 family-supporting jobs.”
TELUS Helps Revitalize City Block
Moreover, as the transformative centrepiece of a revitalized city block, Entwistle says TELUS Sky sets a new standard of excellence in architectural beauty and environmental sustainability, exceeding the global standard for leadership in energy and environmental design.
“We are exceedingly proud that TELUS Sky will continue to build a friendly future for everyone who lives, works, and serves in the great City of Calgary.”
CLICK HERE TO READ THE ENTIRE ARTICLE
Folsom HQ: Economic Development is on the Rise in Technology, Healthcare and Education
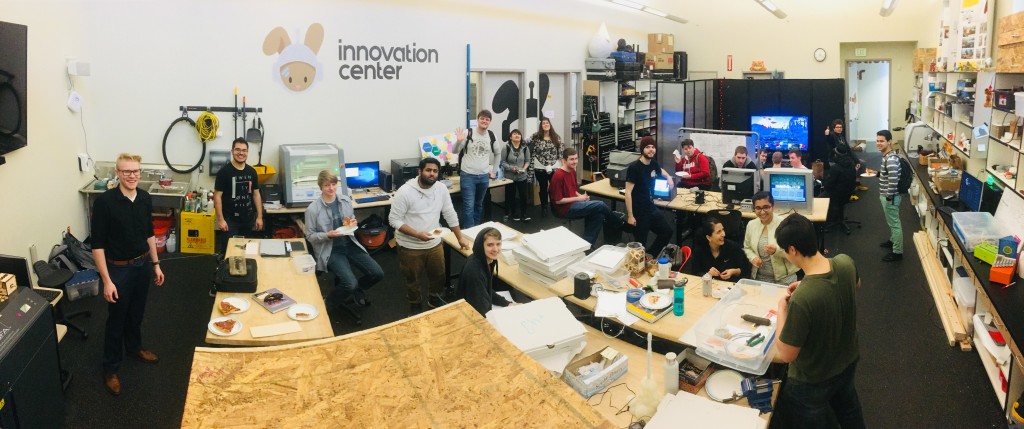
Folsom Lake Innovation Center’s makerspace is a tech-forward hub for students where they can work on projects, share ideas, equipment, and knowledge. Photo: Folsom Lake College
By Lisa Kopochinski
As the cost of living continues to rise in California—particularly in the Bay Area—companies and individuals across the Golden State are looking to relocate to cost-affordable cities or towns.
So, it comes as little surprise that large corporations in many different industries—including technology—are selecting Folsom as a great place to move their headquarters to. The city’s economy is dominated by technology and health care, which are huge employers in the area.
Memphis Metal Museum to Undergo Major Expansion
BY LISA KOPOCHINSKI
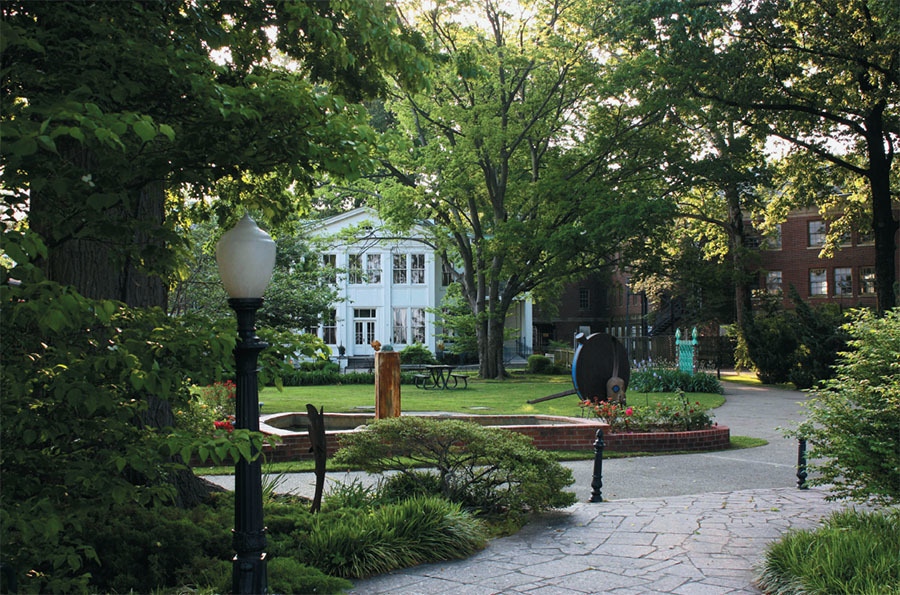
The Metal Museum, located in Memphis, Tenn., and founded in 1979 with NOMMA member support, recently launched a capital endowment campaign to create a new vibrant center to advance its mission to expand its exhibitions, offer more classes and youth programs, and provide additional opportunities for artists.
As the only institution in the U.S. devoted exclusively to the preservation, promotion, and advancement of the art and craft of fine metalwork, the museum is located on 3.2 acres of historic property overlooking the Mississippi River. It includes the main building as well as the metals studios, library and resource center, and private artist residences.
As a center for metal arts, the Metal Museum promotes artists and their work through award-winning exhibitions and advances the education of the public through innovative and active arts programs.
The Metal Museum is in the process of raising $35 million to renovate an 80,000-square-foot building in Overton Park in the heart of midtown Memphis. The renovations include the addition of a new state-of-the-art metals studio to house spaces for forging, casting and large metal fabrication. Under lease terms from the City of Memphis, renovations to create a versatile and vibrant community space devoted to the art of fine metalworking will begin once $25 million has been committed. The campaign also includes $10 million to bolster the Museum’s existing endowment.
At the present time, the Museum has secured more than $16.4 million in commitments. The campaign got off to a strong start with a $12 million commitment from the Windgate Foundation (Little Rock, Ark.). Additional support has been received from ArtsMemphis, the Assisi Foundation, First Horizon Foundation and Hyde Family Foundation, among others.
In the Beginning: NOMMA’s Relationship
NOMMA’s relationship with the Metal Museum dates back 47 years to the 1975 NOMMA conference when members proposed the idea of a national museum dedicated to the collection, exhibition, and preservation of ornamental metalwork.
James “Wally” Wallace is the founding director of the Metal Museum who was hired by NOMMA a couple of years later to get the building ready, oversee volunteers and other responsibilities.
In 1979, the new museum opened its doors to the public. With the addition of a blacksmith shop, foundry, library and resource center, the Metal Museum quickly expanded its mission to preserve, promote, and advance the art and craft of all fine metalwork in all forms.
“It was through NOMMA that this museum came to exist,” recalls Wallace. “We had a real strong working relationship with NOMMA. I recall that Roger Carlsen (president of Ephraim Forge, Inc, of Frankford, Illinois) was very involved on the educational foundation and on the board. There were others involved too. The financial support that NOMMA was giving the museum was critical. There were a number of people who made pledges. The financial funding in those early days primarily came from NOMMA members. Many of the early contributors, however, are no longer with us.”
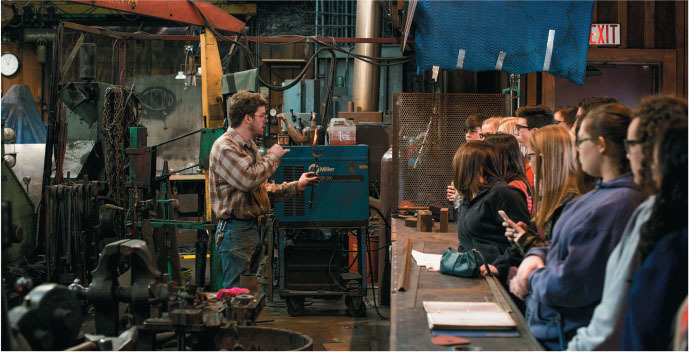
Wallace says that the museum was very involved with NOMMA for approximately 15 to 20 years. “However, we weren’t going to be able to draw an audience on iron alone. We had to expand to other metals as well.”
And, although the collaboration lessened over the years when the museum aspect became the primary draw – drawing focus away from just blacksmithing and fabrication – the NOMMA community remained involved in the Metal Museum through an auction at the annual convention for many years.
Many members have remained strong supporters over years, including the Keeler family (Keeler Iron Works, Memphis, TN); the Lawler family (Lawler Foundry, Birmingham, AL), and Bill and Janice Gasparrini (Post Road Iron Works, Greenwich, CT).
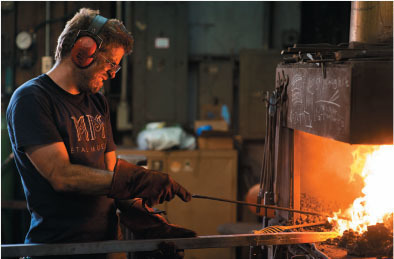
Young students marvel at a casting made by the Foundry at a Metal Museum event.
“Within the last couple of years there are some of us who have had a longstanding relationship with both the Metal Museum and NOMMA/NEF who felt the absence of this once close bond and began the efforts to bring us back to where we once were,” says Roger Carlsen.
“At our own initiative Stacey Lawler Taylor (former NOMMA board member) and I feel we are making great inroads to creating new opportunities for this reunion. I believe it is key to the revitalization that the NOMMA membership be aware of the long-standing connection between the two.”
Current Museum Executive Director Carissa Hussong says the museum has received important gifts from NOMMA members, including a large selection of JG Braun ornaments from Ernest Wiemann, and rare books and archives from Walter Blum (Julius Blum and Company, (Carlstadt, NJ) and Abe Sauer (Tennessee Fabricating, Memphis, TN).
“The Museum has also partnered with the members of the Upper Midwest Chapter on volunteer days at the museum and an iron pour at a chapter meeting at the Lawler Foundry. And, we are grateful for the strong relationships that continue today, including the support and friendship we receive from members like Roger Carlsen and Stacey Lawler Taylor.”
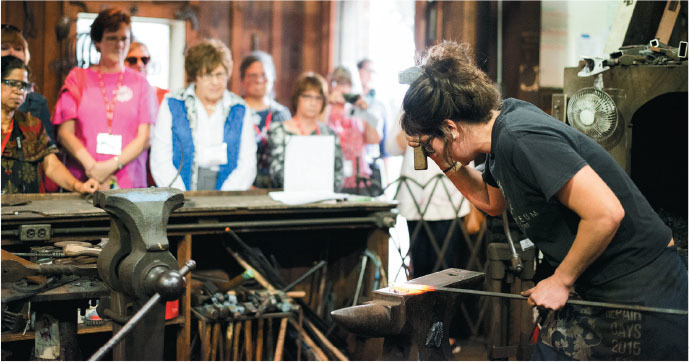
Expansion Details
As the field of fine metal work has grown over the past four decades – and continues to do so – the Metal Museum’s curatorial and collecting activities have not only kept pace, but have contributed to that growth, establishing the Museum as a leader within the field.
For example, the exhibition program celebrates the talent and diversity within the field by showcasing all forms of metalwork and introducing visitors to a wide array of materials and techniques by contemporary artists. Through upwards of 10 originally curated exhibitions each year, the Metal Museum advances the exploration of fine metalwork.
Alongside exhibitions, the Museum holds a collection of contemporary artworks created since the Craft Revival of the 1960s, as well as historic objects, artwork, and drawings, that help visitors understand the history of American metalsmithing. The collection plays an important role in preserving the field of American metalsmithing by documenting the progress, decline, and rebirth of the field and by examining influences on contemporary American metalsmiths.
Dr. Richard Aycock is chair of the Capital Campaign Committee. He says the expansion will allow the Museum to grow and diversify the educational experiences offered and provide new opportunities for everyone – from the world-renowned artist to the rural hobbyist welder to the second grader who has never seen blacksmithing or casting in process.
“The Metal Museum is more than a unique museum with amazing art to see. Through its outreach and education programs, it is also an education center than enhances the entire community through metal arts.”
Hussong concurs and adds, “As the future tenant of Rust Hall, the Metal Museum is elated for the possibilities an expansion of this magnitude provides not only for the museum but for Memphis, the Mid-South and the international metalworking community. We consider this a tremendous honor and responsibility to preserve this mid-century architectural icon and breathe new life into this beloved building in the heart of Memphis.”
The renovation will include an impressive ground floor entrance, and a café with a terrace overlooking the golf course, in addition to a shaded plaza that will provide new connections to Overton Park Shell and the Brooks Museum of Art.
The revitalized 350-seat auditorium will host lectures, films, and musical performances, while an assortment of rooms will be available for meetings and special events. Visitors will also have access to the rooftop terrace that overlooks the Greensward in one direction and the Shell in the other.
Additionally, as part of this impressive project, the Museum will enhance the existing landscape and preserve the Old Growth Forest found in Overton Park, while embarking on new partnerships with other institutions in the park. Through new landscaping and a sculpture grove, there will also be wandering paths around the building.
When completed in 2025, the expansion and renovation will provide the Museum with six times the space for education programs and exhibitions.
The new studios – all under one roof – will offer staff and visiting artists the ability for both greater technical capacity and creation on a wide range of projects. The expansive space will allow for an increased number of traveling metalsmiths for workshops and conferences all in an effort to foster an international community of metalsmiths.
Additionally, larger gallery spaces provide few limitations in the showcasing of a wider range of artwork with respect to height, weight, scope and prominence.
“As a result, both the Metal Museum and Memphis will be increasingly seen as a destination for schools, artists, collectors, and curators interested in metalwork and fine craft,” says Hussong.
Adds Carlsen, “I believe the mission and goals of the two organizations have significant overlap and a longstanding relationship. Creating education opportunities, historical preservation, and bringing new people into the world of metals are just a few of these goals. And, rather than working completely independent of each other, we are both best served in sharing these initiatives.”
Disaster Preparedness: What to Consider
No matter the project location, a robust safety, storm and disaster readiness plan is a must.
By Lisa Kopochinski
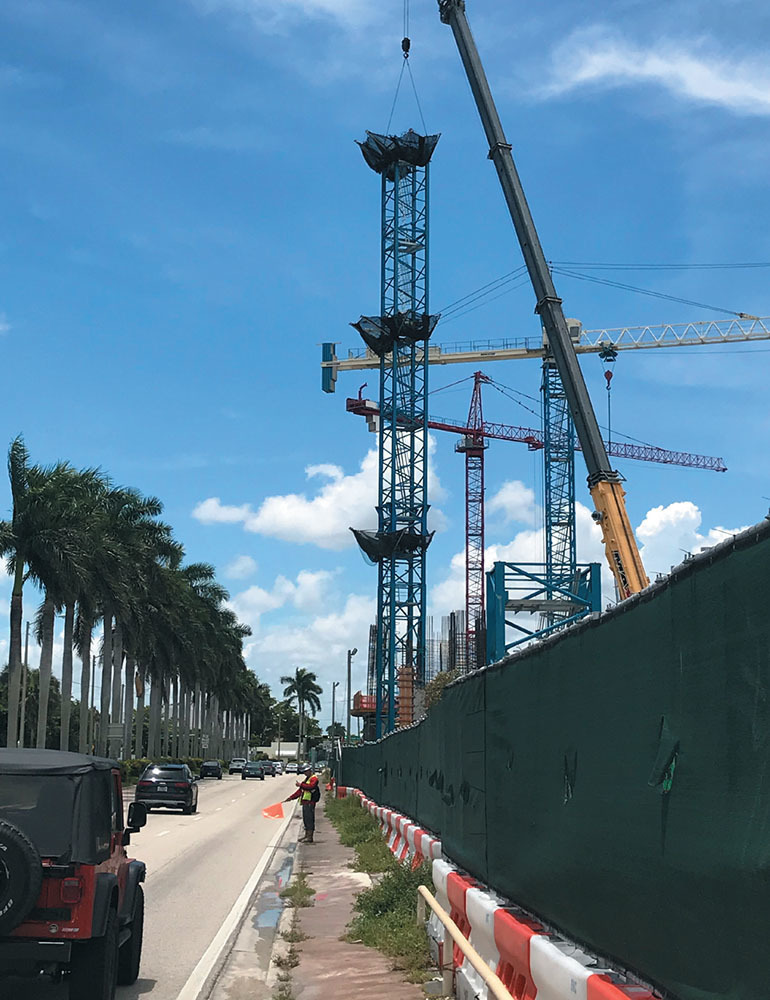
Whoever said that life, death and taxes are the three things in life that are certain forgot to include weather as the fourth.
Just ask anyone in the construction industry, and they’ll tell you that Mother Nature has her own ideas. This is why disaster preparedness is more vital than ever especially if you live and work in an area prone to hurricanes, floods and flash floods.
Extreme Weather
Christopher Diaz is vice president of environmental, health, and safety for Balfour Beatty’s Buildings operations in Florida, and also serves on the South Florida Chapter-AGC board of directors.
He says general contractors need to understand that storm preparedness planning should begin before putting the first shovel in the ground because severe weather — such as hurricanes — is often unpredictable.
“Storms have the potential to intensify and rapidly change paths, so it’s vital for project teams to be well-versed in proactive storm procedures. It’s essential that these plans are communicated and executed in the preplanning phase so project teams can quickly and safely react when unexpected weather approaches.”
Diaz adds that it is equally essential that contractors structure the delivery of projects based on the weather they may have to withstand during and after construction.
“In areas of Florida, we center our buildings operations around wind cycles and hurricane systems, blue sky lightning, heavy rain and flooding to mitigate risk. In this instance, a plan that accounts for securing equipment that the wind can move, such as tower cranes, loose materials, electronics and scaffolding helps protect the project and surrounding infrastructure, and those who come in contact with our work.”
For heavy rain and flooding, Diaz says that sandbags are placed around the perimeter of their project sites to divert turbid, muddy floodwater, and to prevent pollution in local waterway systems.
“Projects located in coastal planes also experience low and high tide sea levels that can rapidly cause flooding. Non-stop de-watering controls may also be necessary to ensure infrastructure is safely out of the ground and protected against corroded building foundations.”
Michael Teng is assistant vice president of regional product, pricing, and underwriting for Sentry Insurance in Stevens Point, Wisconsin. He says when a disaster occurs, the most important thing is getting workers into a safe zone quickly.
For example, if a flood is expected around a team’s project, the safe zone should be in a secure, higher elevation area. Conversely, if a tornado is forecasted, the safe zone should include the lowest area in a secure building.
“If you have more time to prepare for a forecasted disaster, it may allow your business to activate its full business continuity plan like getting critical materials and equipment off the project site, while also designating a temporary work location.”
Creating a Safety Plan
When it comes to instituting a safety plan, the critical areas of disaster preparedness include planning, training and execution. If one of these is missing, it could be extremely costly to a construction business.
“Your geographic region can also influence your preparation and planning,” explains Teng. “If you’re a contractor in the Great Plains, your tornado risk is higher, while a contractor in the southeastern region is more prone to hurricanes. Your plan should reflect the likelihood of disaster types based on your geographic region, but it shouldn’t exclude less common scenarios.”
Eric Yates is the southeast region, environmental, health, and safety manager for Balfour Beatty’s U.S. Civils operations. He says ensuring the team is safe is the most critical aspect of disaster preparedness and post-disaster recovery.
CLICK HERE TO READ MORE:
https://www.constructormagazine.com/disaster-preparedness-what-to-consider/
Project Spotlight: Fireboat Station at the Port of Long Beach
When completed in 2023, the new station building will serve as offices, accommodations, and a maintenance shop for the Port of Long Beach Harbor firefighters.
By Lisa Kopochinski
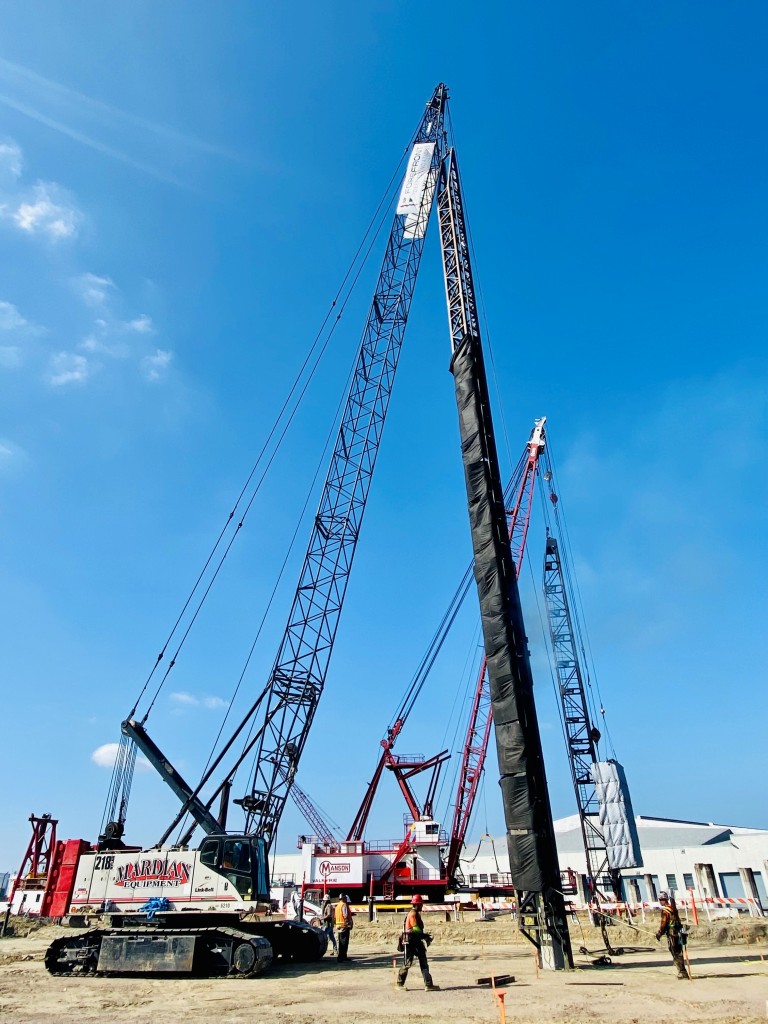
Work remains well underway on the new Fireboat Station project for the Port of Long Beach Fire Department in Long Beach, Calif.
With a completion date slated for Spring 2023, Forefront Deep Foundations began probing work on the $31.6 million project in Spring 2021.
“This project is a result of significant port expansion within recent years,” explains Jeff Bird, President of Forefront Deep Foundations, a PDCA member company based in Newport Beach, Calif.
“This site is located at Pier Berth D50 at Pier D where the site has served multiple purposes since it was originally developed in the 1920s. Based on geotechnical investigations of the site, it has been discovered that the new Fireboat Station site is underlain with an existing quay wall, timber piles, a timber wharf structure, and miscellaneous concrete structures.”
In order to provide proper foundation support for this project, Corner Structural Engineering designed the boat house dock to be supported on 24-inch concrete octagonal piles, and the Fireboat Station to be supported on 16- inch concrete square concrete piles.
“Forefront’s role was to furnish and install the landside piles for the new Fireboat Station building,” says Bird. “The building will serve as offices, accommodations, and a maintenance shop for the Port of Long Beach Harbor firefighters.”
Scope of Work
Forefront Deep Foundation’s scope of responsibilities on this impressive project included the following:
- Performing probing and pre-drilling work at all future pile locations;
- Furnishing and installing 16-inch square concrete piles for the Fireboat Station Building while meeting project noise mitigation requirements;
- Cut-off piles in 1-foot to 25-foot lengths that reached refusal during installation, and;
- Furnishing and installing epoxy coated # 8 anchor bars in dowel tubes that were in the piles.
The company began probing work last spring and completed the project (dowel installation) last fall. The team used the following piledriving equipment on this project:
Pile Probing
- APE 150 Vibratory Hammer
- 90-ton RT Crane
Pile Driving:
- APE D-36 Diesel Impact Hammer with 26-inch swinging leads
- Link-Belt 218 110-ton Crawler Crane
- Custom-made sound blanket attached to pile driving leads to meet rigorous sound mitigation requirements
As for the number of piles driven for the actual foundation, Bird doesn’t miss a beat.
“Forefront installed 78 total 16-inch square concrete piles in 15-foot to 78-foot lengths for the Fireboat building. The first pile installed had Pile Driving Analyzer (PDA) monitoring in order to confirm that the required pile design capacities had been met. Manson Construction—the water piledriving contractor—installed 77 total 24-inch octagonal concrete piles in 86-foot to 100-foot lengths for the Fireboat dock.”
Project Challenges
From a piledriving standpoint, this project did present some unique challenges for the team.
“For example, there were challenges with installing piles on a site with existing wharf structures, timber piles, and concrete structures built in the 1920s and 1930s,” explains Bird.
“This required ‘probing’ 35 feet in depth to find the top of the wall elevation prior to determining the pile lengths, which ranged from 30 feet to 78.5 feet.”
The project also had stringent noise mitigation requirements that exceeded the specifications of typical sound blankets.
“In order to meet the project requirements, Forefront had to get creative,” recalls Bird.
“We developed a system that was comprised of a mass loaded vinyl material for Sound Transition Class Rating (STC) attached to two layers sound blankets for Noise Reduction Coefficient (NRC). This custom fabricated system of combined materials met the sound mitigation requirements of .9 NRC and a 28 STC. The system worked fantastic throughout the duration of the project. I’m proud of our team’s innovation to successfully solve this challenge. That’s what we do best—address and solve challenges.”
Forefront was also required to pre-drill and probe at all pile locations as a preliminary phase of work in order to determine the depth of existing structures.
“There was great concern that if the piles were too long, they would damage the existing quay wall, which was believed to be 20 feet to 30 feet below existing grade,” says Bird.
“Upon review of the data from the probing and drilling, the geotechnical engineer provided the concrete pile cast lengths for the future Fireboat Station Building.”
There were also strict local hire and apprentice requirements where each contractor was required to hire workers within a 50-mile radius of the project.
“We were able to work with the Pile Drivers Local 562 based out of Long Beach to ensure that this requirement was met,” says Bird.
“In addition, Forefront employed multiple apprentices in order to meet the ratio requirements for this specific project. We were very proud to be able to employ apprentices on this project who will one day become the future leaders in our industry.”
Additionally, there was also a mandatory small business requirement on this project to have 20 percent participation of contract value.
“Due to the fact that Forefront Deep Foundations is a certified Small Business Enterprise by the California Department of General Services, we were able to contribute 100 percent of its contract amount to assist in meeting the general contractor’s SBE requirements,” says Bird.
In all, he adds that Forefront is honored to work on a project that will benefit our country’s first responders.
“We were proud to be able to employ apprentices on this project who will one day become the future leaders in our industry.”
Escalator Tax Draws Critics
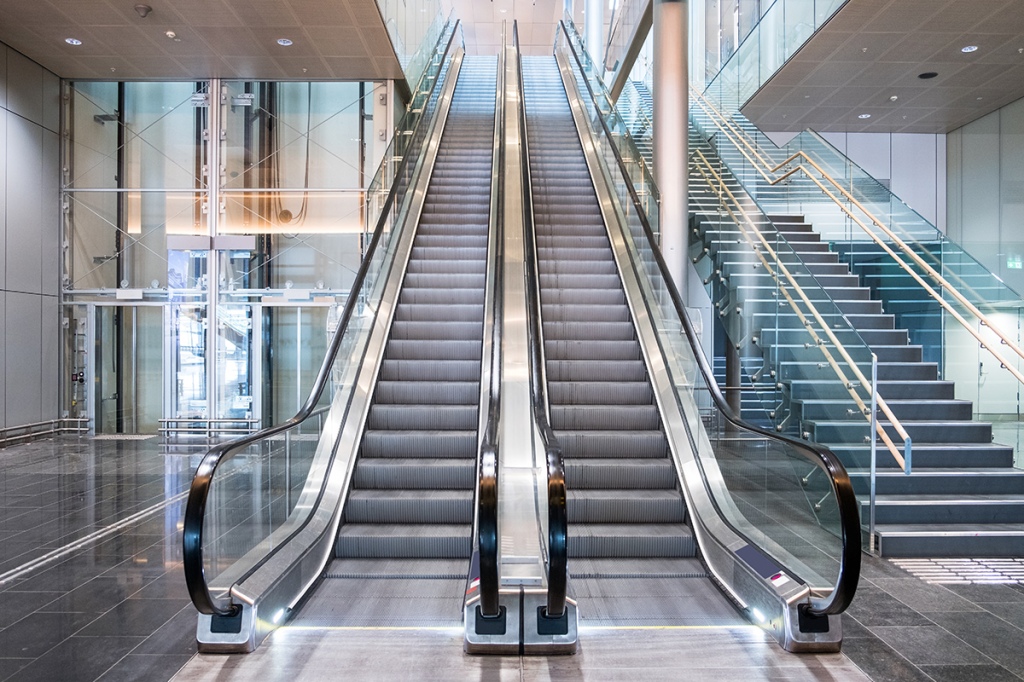
By Lisa Kopochinski
In 2017, the Government of Canada quietly slid an automatic tax escalator mechanism into legislation, which imposes an automatic hike to excise duty rates on all beverage alcohol every April 1.
By Lisa Kopochinski
Canada is known for many wonderful things. Having one of the highest taxation rates on alcohol in the world is probably not one of them. For example, 47 per cent of the price of a bottle of beer is tax, while for a bottle of Canadian whisky or other spirits, 80 percent of what consumers pay is tax.”
Yet, on April 1, 2018 an “escalator tax” was introduced that automatically increases the tax rate annually. Suffice to say, this was no April Fool’s joke. Many in the industry are not pleased and are loudly opposing this recurring annual increase.
“At 47 per cent of the price already, we believe Canadian beer drinkers pay enough tax on their beer,” says Luke Harford, president of Beer Canada, an Ottawa-based association that is the national voice of beer, representing more than 50 Canadian brewing company and 90 per cent of beer made in Canada. The association is a leading proponent in the moderate and responsible consumption of alcohol.
“Canadians pay one of the highest beer taxes in the world. The tax on beer is five times higher here than it is in the U.S. Here, you pay $20 in tax on a case. In the U.S. you pay just $4. Our beer industry is threatened by runaway taxes, yet in the spring of 2017—with no industry consultations or economic assessments—the Government of Canada quietly slid an automatic tax escalator mechanism into legislation which imposes an automatic hike to excise duty rates on all beverage alcohol every April 1 by the rate of inflation.”
CLICK HERE TO READ MORE
Career Story: Sarah Sava of Clark Foundations
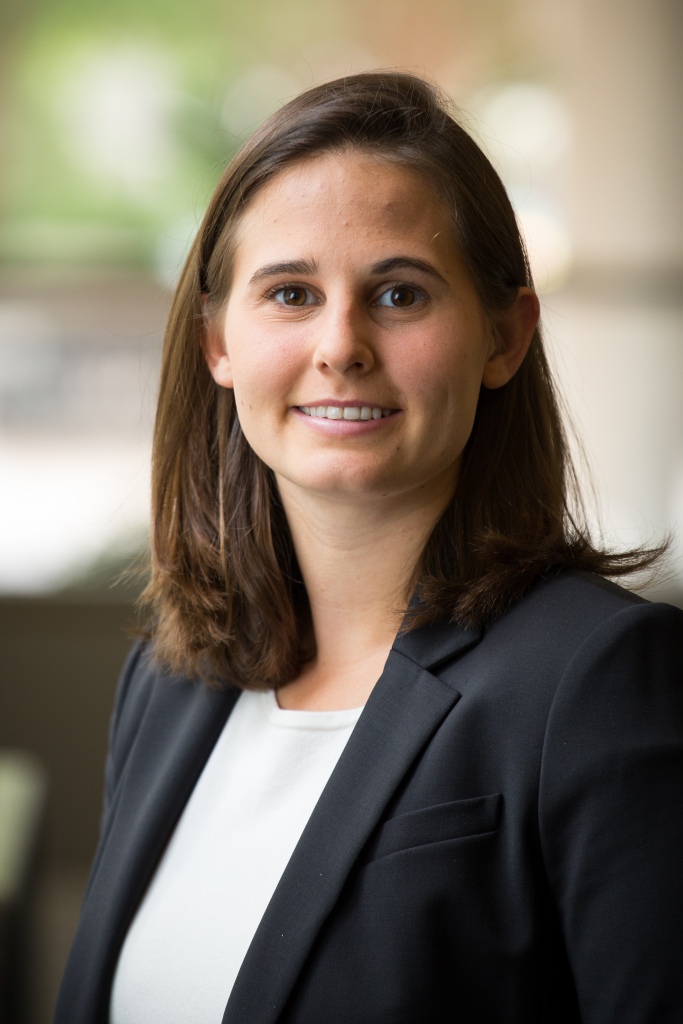
This ambitious project manager leads deep foundation projects from the design/estimating phase through the construction process.
By Lisa Kopochinski
Sarah Sava knew years ago as she pursued a civil engineering degree at the University of Maryland that a career in project management in construction was for her. So, when she joined Clark Foundations in 2013, this confirmed that she had made the right choice.
“I got experience working at my current company through a summer internship program while in college,” she recalls. “I loved getting to work out in the field, getting muddy, while still applying my civil engineering degree.”
From that very first day at Clark Foundations to today, she sees constant examples of how team dynamics impact a project.
“I understood early in my career the importance of coordinating with team members to tackle problems and successfully complete a project. That—
combined with my organizational inclinations—led me to continue along the project management path at Clark after my first few years.”
CLICK HERE TO READ MORE:
http://www.lesterfiles.com/pubs/PDCA/digital/2022/issue1-2022/#p=67
Fatigue Management
By Lisa Kopochinski
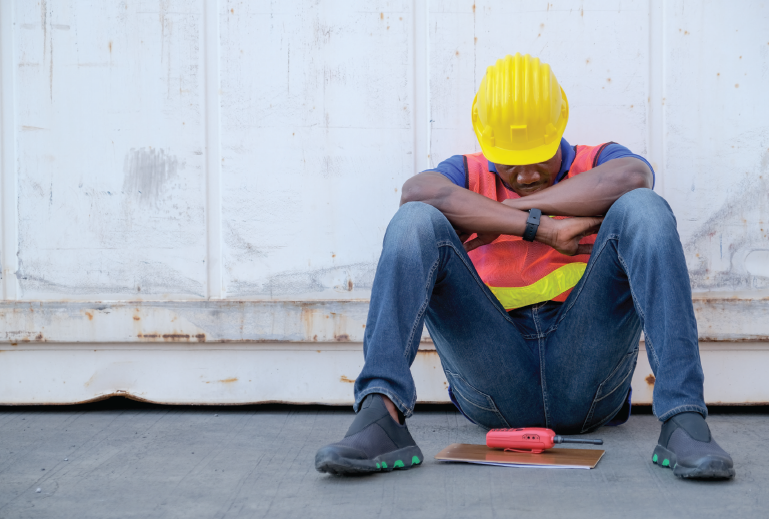
Long hours and hard, physical work are the norm for many working on Canada’s deep foundation construction projects. However, if not properly managed, these conditions can lead to worker fatigue, resulting in unsafe working conditions. This is why companies need to take stronger measures to prevent fatigue.
So, what is fatigue management and why is it needed?
“Basically, it recognizes that fatigue compromises a person’s ability to function both physically and mentally, and even affects our emotional state,” said Mike Harnett, owner and president of Solaris Fatigue Management, a British Columbia-based firm that supplies innovative and effective fatigue risk management strategies.
“The consequences of that are that we cannot continue to function at a level that we need to function at to do the job safely,” she said. “This means more injuries, more incidents, more errors and even more mental health issues.”
While many jobs have hazards attached to them, it is important for companies to take a closer look at how much riskier construction jobs are if the worker is tired.
“The earlier they can become involved, the better,” Harnett said. “At the beginning of the project life cycle, we need to start looking at wherever there is a human interaction, and we need to examine that interaction for hazards. So, if they are looking at where workers are doing the pile driving activities, what are the performance requirements that have to be done?”
Fatigue is normal
What happens if a tired person is placed in line with the hazards of their job? How much riskier do those projects become?
“We need to start looking at our jobs through a fatigue lens,” Harnett said. “Fatigue is part of the normal human condition and it’s not something we are going to eliminate from the worksite. We’re not going to stop people from showing up tired for a variety of reasons, but we can manage it. We have to look at how we design work and manage the risks in order to get them down as low as possible.”
CLICK HERE TO READ MORE
http://www.pilingcanada.ca/tagged/issue-2-2022/fatigue-management-for-deep-foundations-professionals